In hospitals, every second matters — nurses rush between rooms, physicians consult on critical cases, and patients anxiously await their turn. Lean healthcare offers a way to bring order to the chaos and transform how care is delivered.
Imagine a patient arriving at the Emergency Room with severe abdominal pain. In a traditional healthcare setting, they might face long wait times, unnecessary paperwork, and clashes between departments. But with lean healthcare, the patient is quickly triaged and directed to a dedicated care team following standardized procedures to minimize delays.
At its core, lean healthcare is built on a few key ideas:
➜ Lean Principles: Maximizing value for the patient while minimizing waste is the driving force. Healthcare professionals are empowered to identify and eliminate non-value-added activities continuously.
➜ Value Stream Mapping: By mapping out the entire patient journey, from admission to discharge, inefficiencies and opportunities for improvement become clear.
➜ Waste Reduction: Any activity that doesn’t add value to the patient’s care is considered waste – whether it’s excessive waiting times, unnecessary movements, or redundant processes. Lean practices help healthcare systems identify and eliminate these wasteful activities systematically.
➜ Continuous Improvement: Lean healthcare is a process that keeps going. It means finding ways to do better, putting those ideas into action, and checking how well they work. It is a process of constant improvement to achieve better results for patients.
➜ Patient-Centered Care: Lean focuses on putting the patient at the center of all processes and decisions. By cutting down on waste and making processes easier, healthcare workers can concentrate on giving the best care experience.
👑 Experience Lean Healthcare Transformation with BellMedEx
Our expert medical billing services eliminate waste at every step, from coding to collections. We map your revenue cycle, identify inefficiencies, and implement lean workflows – boosting productivity and profits. Outsource billing to us and watch patient satisfaction soar.
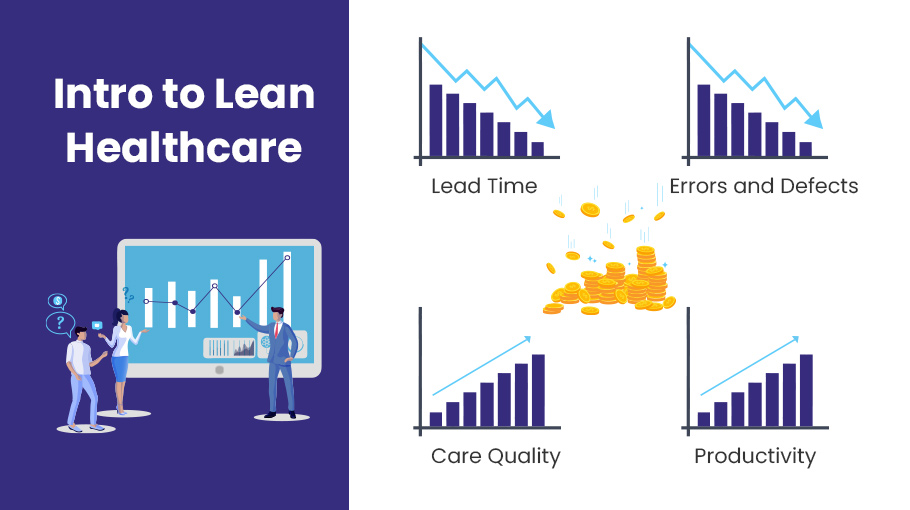
Overview of Lean Healthcare
The concept of “lean” originated in manufacturing, with the term coined by John Krafcik in 1988. James Womack and colleagues later defined lean more broadly in 1996 as a “systematic approach to identifying and eliminating waste (non-value-added activities) through continuous improvement by flowing the product at the pull of the customer in pursuit of perfection.”
The Triple Aim of US Healthcare was created by the Institute of Health Improvement (IHI). It provides a helpful framework, pushing healthcare systems to simultaneously improve patients’ experience, population health, and per capita costs.
While lean has proven models, each organization must modify these models to suit their own context. Establishing a mindset of constant improvement at all levels is necessary for success. When done correctly, lean healthcare methods can greatly transform care delivery.
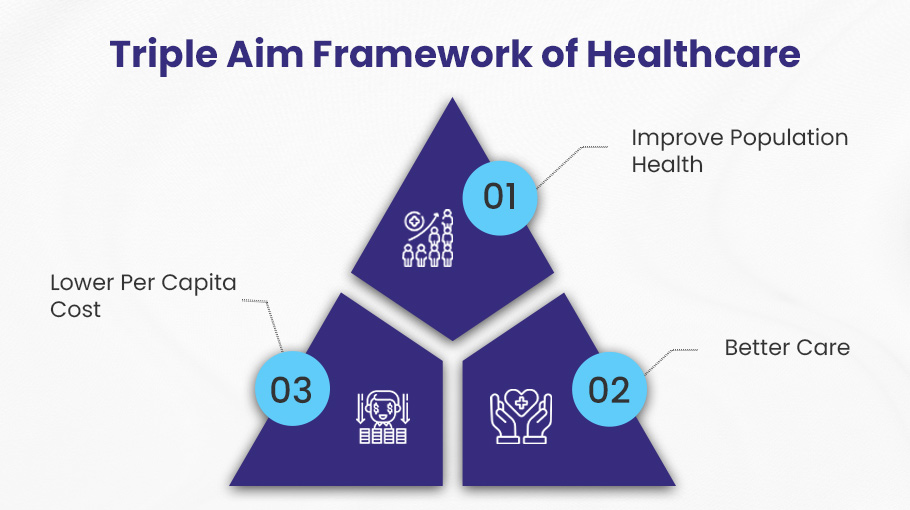
Here are some of the definitions of lean healthcare by different Authors:
➀ Black and Miller (2008):
❝Lean healthcare is a patient-focused approach to managing and delivering care that continuously improves work processes. All aspects of the care delivery system are focused on eliminating waste while steadily increasing value-added work. It is premised on the idea that healthcare can be continuously improved without adding more money, staff, space, or inventory.❞
In simple terms, Black and Miller explain lean healthcare as a way to put patients first. It aims to make processes better by removing waste and adding value for patients, all without needing more money, staff, or space. The main idea is that we can make healthcare better by improving how things are done, not just by adding more resources.
➁ Poksinska (2010):
❝Lean healthcare involves understanding what adds value for patients and eliminating waste from care delivery. It often emphasizes that current healthcare systems have fragmented, inefficient processes that require redesigning the flow of patient care.❞
Poksinska highlights that lean healthcare revolves around understanding what is valuable for the patient and eliminating wasteful activities or inefficiencies in care delivery. She points out that today’s healthcare systems often have broken and slow processes. These need to be changed to make patient care better.
➂ D’Andreamatteo, Ianni, Lega, and Sargiacomo (2015):
❝Basic Principles – Specify value from the patient’s perspective, map the value stream, enable uninterrupted workflow, allow patients to pull value, and continuously improve.
Other Principles – Involve all staff in improvement, respect all employees, and integrate suppliers into the value stream.❞
These authors explain important ideas about lean healthcare. The main ideas are: understand what is valuable for the patient, outline the steps to provide that value, keep the workflow smooth, allow patients to start the value delivery, and always work on making processes better. Also, they say that other important lean principles are getting everyone involved in making changes, treating workers with respect, and bringing suppliers into the value stream.
Waste Categories Used in Lean Healthcare
In lean healthcare, waste is anything that does not help make the patient’s care and experience better. Lean principles aim to find and remove wasteful elements, making operations easier and improving efficiency in healthcare.
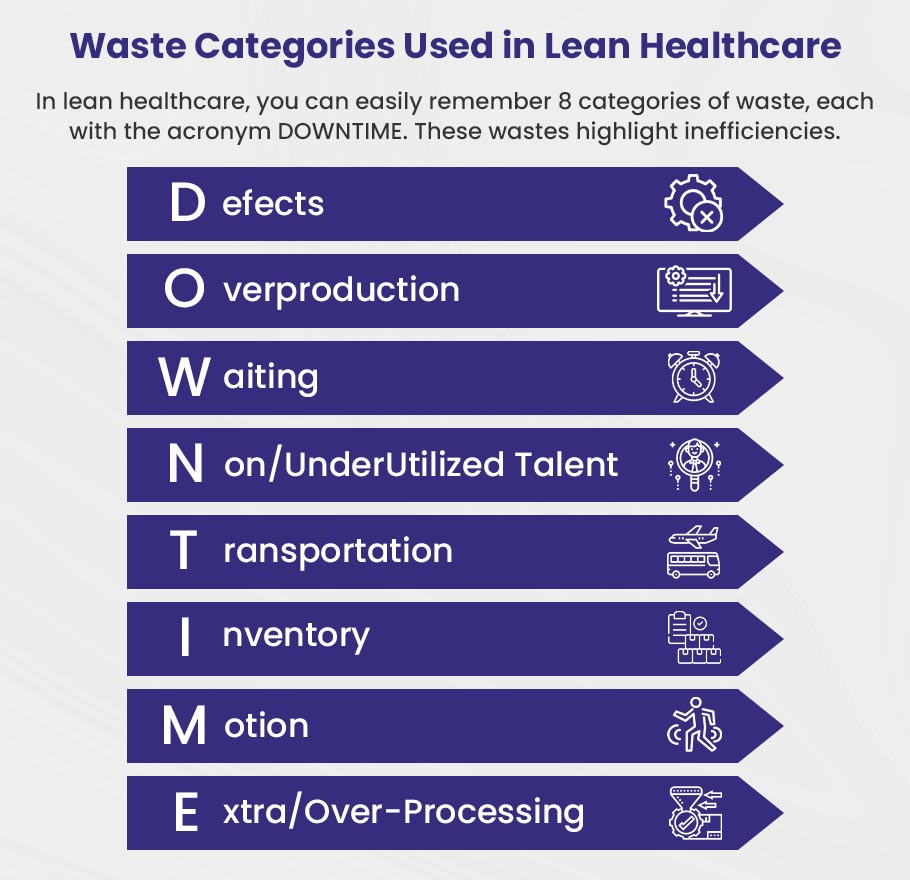
The concept of waste in lean healthcare is often categorized into eight types:
Defects
Errors can happen in medical procedures due to wrong diagnoses or faulty medical equipment that need fixing. These problems can raise costs, harm patients, and slow down medical care. For example, if a patient is diagnosed incorrectly, it can result in the wrong treatment. This may lead to serious health complications and higher medical costs.
Overproduction
If we make more medical equipment and medicine than we need, it creates waste. This waste can include unnecessary diagnostic tests or treatments that are not needed for patient care. For example, doing too many blood tests for a patient when they are not needed wastes resources and incurs more healthcare expenses.
Waiting
If patient care is delayed because of more waiting time for consultation, test results, medical equipment, or doctor availability, this issue can cause long stays of patients in hospital territory and neglect care about patient satisfaction. For example, a patient in the Emergency Room (ER) waiting for many hours to see a doctor may feel discomfort.
Non/Underutilized Talent
Not using the skills and knowledge of medical staff well can cause many problems for healthcare practices. Because of mistakes and low spirits, healthcare workers cannot achieve their best. For example, a nurse trained specifically in wound care might be tasked with recording daily patient visits and discharges, rather than focusing on the specific needs of patients.
Transportation
Transportation is considered the unnecessary movement of patients, staff , or other medical material within healthcare practice. Moving patients between departments without a good reason can be a waste. For example, moving a patient many times for tests can increase the chance of errors and cause more discomfort.
Inventory
Having too few or too many healthcare supplies and medications can hurt patient care. Having too many medical supplies or medications can result in more items getting expired. On the other hand, not having enough can lead to long waits for patient care. For example, having too much medical stock that expires before all items are used can cause money loss. Also, delays in treatment due to inventory shortage can have serious effects or even lead to death.
Motion
Staff may lose time and work less efficiently because of extra physical movement. This can cause poor patient care and wastage of time. For example, a nurse hired for checking patients’ Blood Pressure (BP) spends too much time locating the BP apparatus instead of helping the patient with their worries. In that case, this can disturb the overall productivity of staff.
Extra or Over-Processing
Doing extra work that is not needed, like unnecessary tests, can raise medical costs and slow down patient care without helping anyone. For example, duplicating the same patient information in different treatment forms can lead to more mistakes and extra work for staff.
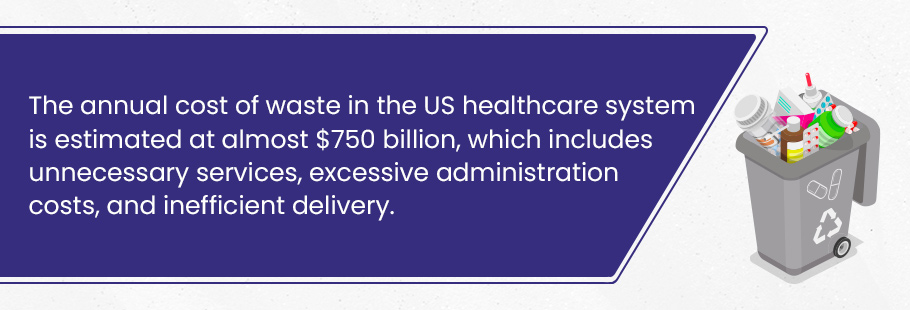
The annual cost of waste in the US healthcare system is estimated at almost $750 billion, which includes unnecessary services, excessive administration costs, and inefficient delivery.
🤑 Unlock Lean Healthcare with BellMedEx Medical Billing Services
Don’t let bloated billing processes hold you back. Our lean medical billing service is the game-changing solution. We get rid of waste and obstacles in your income cycle by streamlining it. Give us the billing duties so you may focus on improving patient care.
Six Principles of Lean Healthcare
Focusing more on better teamwork and working together is very important when using lean healthcare principles. Healthcare practices should improve their use of lean principles. They need to look for ways on finding areas to improve and use data to help them. Using lean healthcare ideas can help your clinic create a stable and balanced environment that offers high-quality, waste-free care.
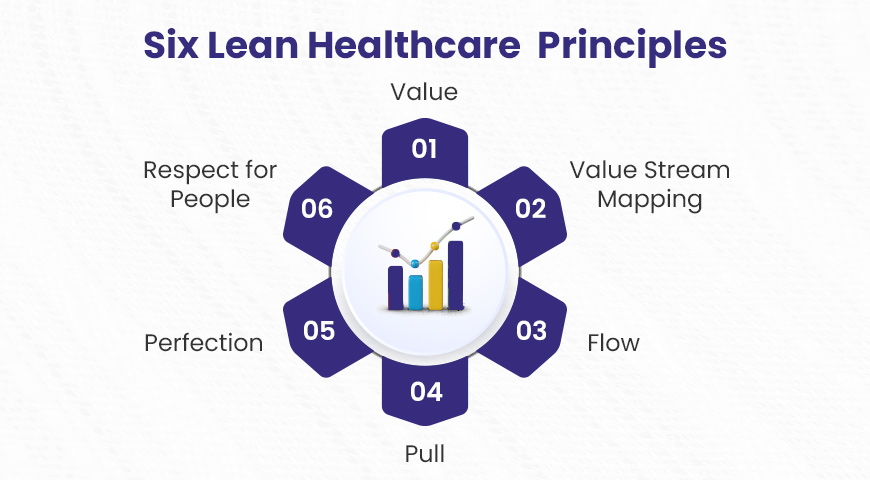
1). Value
It is important to understand what is valuable for treating patients from their point of view. This principle is about finding and providing healthcare services that can help improve patient care and make patients happier. Focusing on what patients need in healthcare can remove unhelpful activities and improve the overall experience for patients.
2). Value Stream Mapping
Value stream mapping shows all steps in a process to find and remove waste. We can look at the whole process from when patients arrive to when they leave. This helps healthcare providers make everything work better and ensure patients move through the system easily.
3). Flow
This principle helps all healthcare processes work well without any problems. It can also highlight the ongoing flow of patients, their information, and medical supplies or medications. By removing all delays and problems, healthcare practices can make wait times shorter and improve healthcare services.
4). Pull
A pull system is a way of providing healthcare services based on what patients need, instead of having set appointments or pre-planned schedules. This principle helps prevent making too much and makes sure all resources are used properly and effectively, which leads to better care for patients and better management of resources.
5). Perfection
Always try to improve all healthcare processes. This principle emphasizes the importance of ongoing evaluation and improvement. It encourages all healthcare providers to always look for ways to enhance quality, reduce errors, and increase efficiency.
6). Respect for Everyone
It is important to recognize and value the contributions of all healthcare staff to keep quality care. This principle aims to create a helpful work environment where all staff can share their ideas to improve processes. When healthcare organizations keep a good culture, they can improve patient care and make staff happier.
👨🏫 Do You Know ➜ What is Lean Six Sigma?
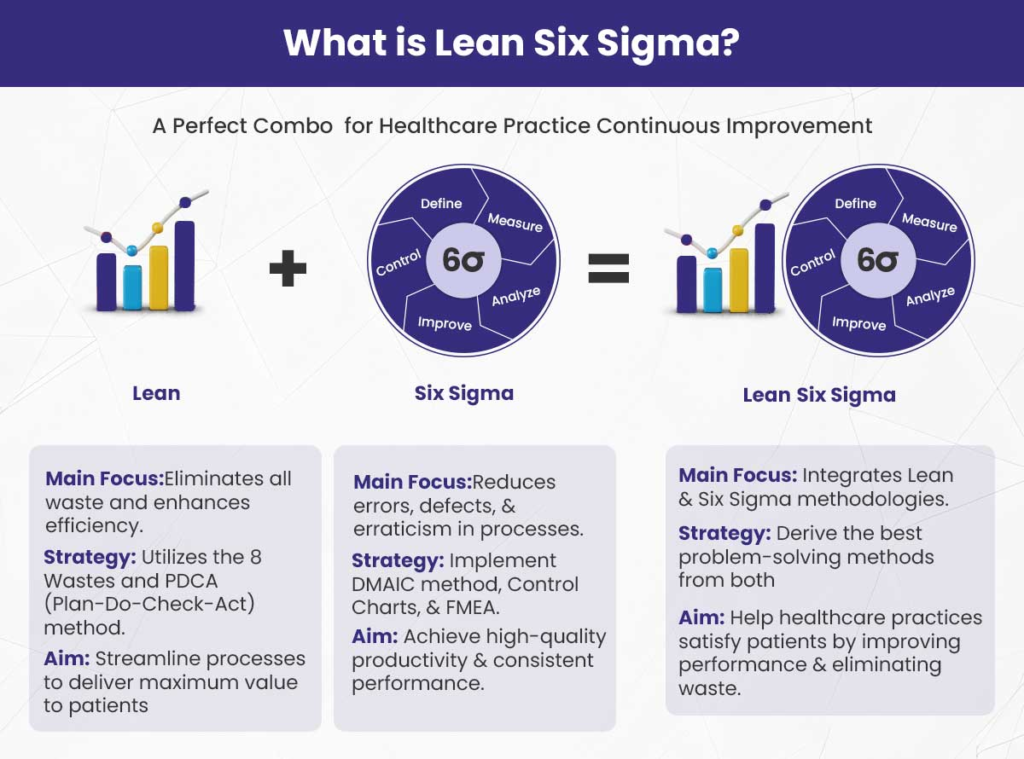
Lean Six Sigma is a powerful approach used in healthcare to make processes better and increase patient happiness. It is a combo of two different approaches: Lean, which works to remove waste and make operations more efficient, and Six Sigma, which seeks to lower mistakes and enhance quality. Lean uses tools such as the 8 Wastes and the PDCA cycle. Six Sigma uses the DMAIC method to define, measure, analyze, improve, and control processes.
Similar to a thriving garden where each plant contributes to the ecosystem, Lean and Six Sigma work together to help healthcare practices provide better services. They improve performance, reduce waste, and make sure the quality is always up to the mark.
Lean Methodologies and Implementation in Healthcare
Lean methodologies and how to use them are important for better patient care, making operations work better, and cutting down on waste. Here are different methodologies that are used to make the healthcare system better.
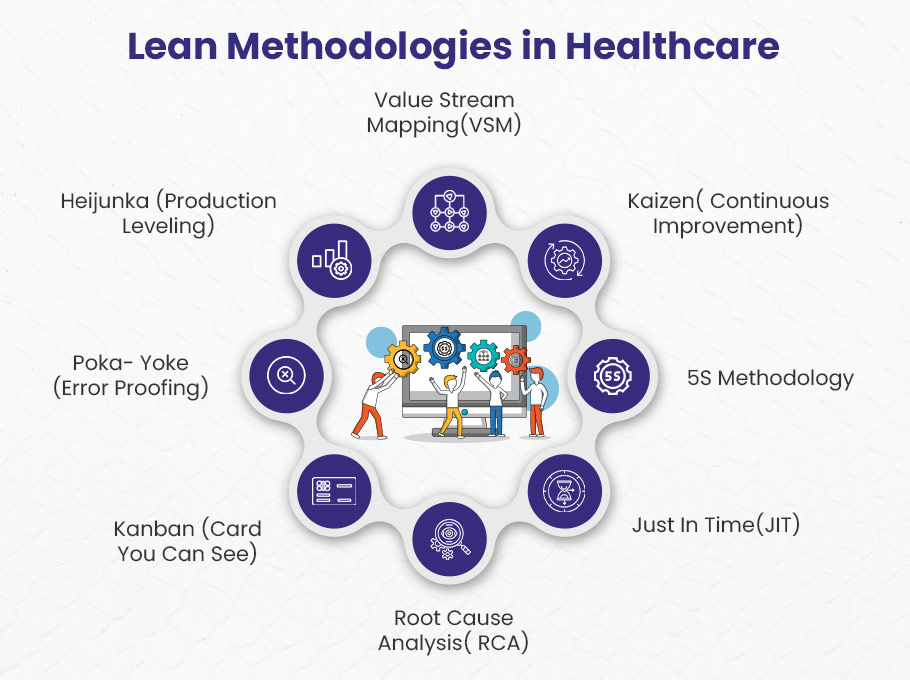
1). Value Stream Mapping (VSM)
Value stream mapping is a useful tool that healthcare organizations can use to make patient care better. It shows a clear picture of the whole process of giving care to patients, from beginning to end. This covers all tasks, like ordering supplies and administering medicine. The map helps teams find problems, waste, and things that do not work well so they can fix them. This simple process lowers costs and waiting times and makes care better.
VSM Implementation in Healthcare
Healthcare providers make a value stream map by looking at each stage of the patient journey. This shows the value-added and non-value-added parts at each stage. Value-added steps help patients feel better, such as tests to find out what is wrong and treatments to help them recover. Non-value-added steps are activities that waste time and do not help improve care. Examples include patients waiting for appointments or having to fill out lengthy paperwork.
With this bird’s eye view, the healthcare team can redesign workflows to maximize value-added steps and minimize waste. Patients benefit from smoother, faster and higher quality experiences. Providers benefit from reduced costs and better utilization of resources. It’s a win-win for all through smarter delivery of care.
2). Kaizen (Continuous Improvement)
Kaizen is a process of constantly looking for ways to improve. It involves everyone in an organization working together to make small, incremental changes on a daily basis. The goal is to eliminate waste and streamline processes.
In healthcare, Kaizen can help make the movement of patients in a clinic better. A team plans every part of the patient journey, starting from checking in, to seeing the doctor, and ending with checking out. They find problems or slow parts in each stage and think of ideas to make the process easier. This could be as easy as moving furniture around or adding signage. Kaizen means making small changes all the time, not big changes all at once.
Kaizen Implementation in Healthcare
Kaizen encourages all healthcare workers to share their ideas for making patient care and satisfaction better. Each day, a quick team meeting can be held to talk about issues that came up the day before and possible solutions. Or a suggestion box can be used for staff to share provide their input anonymously.
Implementing Kaizen means building a culture where people always learn and get better. Leadership must be open to ideas from nurses, technicians, billing staff, and everyone else. Small changes suggested and tested by frontline staff often have the biggest impact.
3). Just In Time (JIT)
The Just In Time (JIT) method means getting supplies and materials only when you need them, rather than stocking up in advance. The goal is to avoid overproduction and excess inventory, which can cause waste. With JIT, you make or order just what is required, just when it is required. This helps save money and improve efficiency.
JIT Implementation in Healthcare
Healthcare providers can use the JIT method to handle supplies and medicine. Instead of keeping a lot of extra supplies based on guesses about what will be needed later, healthcare practices can buy drugs and medical items based on what they actually use each day. A clinic pharmacy can count how many prescriptions are filled each day for specific medicines. It can then order more from suppliers to meet this need. This prevents over-ordering and expired drugs. It also lowers the need for storage and cuts down inventory costs. The key is having an accurate understanding of daily needs, and a responsive ordering process.
4). Root Cause Analysis (RCA)
Root Cause Analysis is a way to solve problems in healthcare. It helps find the main reasons for issues. It means looking into problems to discover the real reasons why they happened. The purpose of RCA is to discover ways to stop problems from happening again.
RCA Implementation in Healthcare
RCA helps us find out why a medication mistake happened. For example, if a patient gets the wrong amount of medicine, the healthcare team looks closely to understand how the mistake happened. They might find that the drug labels were not clear, nurses had too much work, or there was confusion among the staff. Finding the root cause helps the hospital make clear changes, like updating labels, changing nurse schedules, or improving handoff procedures. This helps prevent similar medication mistakes in the future and makes patient safety better.
5). Kanban (Card You Can See)
Kanban is a way to see and manage work as it goes through different steps. It uses cards or signals to show tasks or work items that go through different steps from beginning to end. The goal is to visualize workflow, limit work-in-progress, and maximize efficiency. Think of a Kanban board with sticky notes moving across columns to understand when something is ready to be worked on, in progress, or completed.
Kanban Implementation in Healthcare
A hospital can use Kanban cards to track patients as they go through different departments. A card can show a patient going from being admitted, to getting tests, to having surgery, and then to recovery. This gives staff an easy way to see where patients are and what still needs to be done.
For supplies, color-coded cards can indicate which surgical instruments or medications are running low. This signals to staff what needs to be reordered without excessive overstocking. Patients get what they need, when they need it, without supplies expiring on shelves.
6). Poka-Yoke (Error Proofing)
Poka-Yoke is a lean methodology that helps stop mistakes before they happen. It focuses on building quality into processes by adding simple fail-safes that make errors nearly impossible. The goal is to design systems where the next logical step is the correct step. This eliminates the need for expensive defect detection and inspection processes down the line.
Poka-Yoke Implementation in Healthcare
Poka-Yoke can help healthcare organizations reduce medical errors that put patients at risk. Some examples include barcode scanning to verify that patients receive the right medication and dose, surgical checklists to confirm all instruments are accounted for, and alerts that sound when improper dosages are entered into IV pumps. These simple mechanisms make it harder for staff to make mistakes that could lead to patient harm.
Poka-Yoke shifts the focus from blaming individuals for errors to creating systems that are mistake-proof. This contributes to a culture of safety and continuous improvement in healthcare. When errors can’t occur in the first place, outcomes improve and costs decrease.
7). Heijunka (Production Leveling)
Heijunka is a lean methodology that aims to smooth out the flow of work over time. It involves leveling the mix and quantity of production across a time period. The goal is to eliminate unevenness, overburden and waste. Heijunka creates a steady predictable pace so operations can work at an optimal volume. This helps reduce variability and stress on the system.
Heijunka Implementation in Healthcare
Heijunka can help healthcare providers better manage their workload. It involves carefully scheduling the type and number of procedures during a week or month. This balances out the workflow instead of having huge backlogs on some days and empty schedules on others. For example, a surgeon can space out surgeries evenly rather than cramming them all on certain days. This avoids overburdening staff with too much work on busy days. It also reduces patient wait times since work is spread out predictably. Heijunka allows healthcare teams to operate smoothly at an optimal pace.
💫 Cut The Wait, Not The Care ft. BellMedEx Medical Billing Services
Long hold times and billing hassles are wasting your resources. Our lean medical billing cuts out delays and blockages so you can invest in patient care. Partner with us and achieve new heights of efficiency.
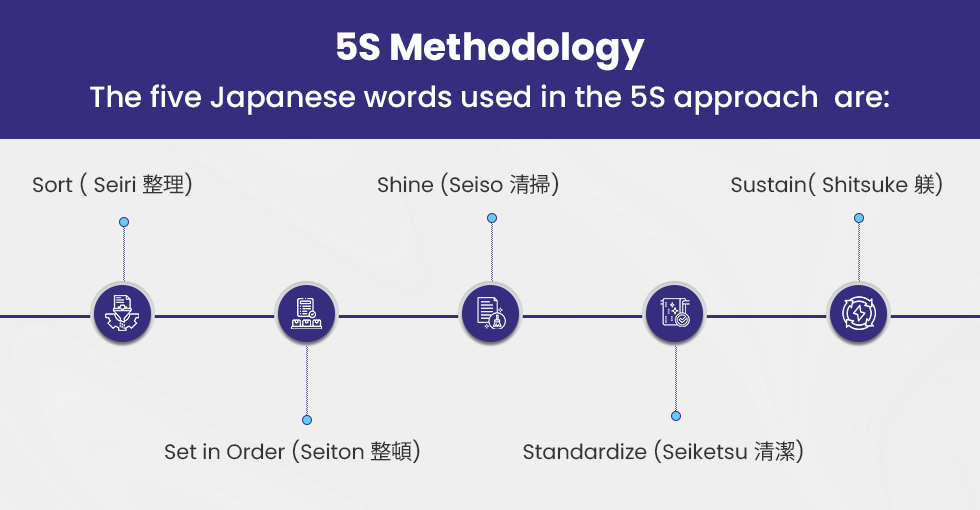
What is 5S Methodology in Lean Healthcare?
The 5S methodology is a lean approach that aims to improve workplace efficiency, safety, and organization in healthcare settings. It consists of five Japanese principles, each starting with the letter “S”:
1
Sort (Seiri 整理) — Identify and eliminate unnecessary items from the workspace, keeping only essential medical supplies and equipment.
2
Set in Order (Seiton 整頓) — Arrange and label all necessary items in a systematic and logical manner for easy access and retrieval.
3
Shine (Seiso 清掃) — Maintain a clean and hygienic work environment by regularly cleaning and sanitizing medical equipment, workstations, and patient areas.
4
Standardize (Seiketsu 清潔) — Establish and implement consistent procedures and standards for tasks such as inventory management, equipment sterilization, and patient intake processes.
5
Sustain (Shitsuke 躾) — Continuously review and improve the established standards through regular audits, training sessions, and encouraging staff to adhere to and enhance the 5S practices.
Examples of Lean Healthcare
The following are some easy examples of how lean healthcare can help improve healthcare practices and make managing tasks easier:
Example #1 ➜ Reducing Wait Times in the Emergency Room
Have you ever had to wait for hours in the emergency room before being seen? Lean healthcare can help reduce those long wait times. Hospitals use a method called Value Stream Mapping to map out the entire journey a patient takes from walking in the door to being discharged. By streamlining the processes in the emergency department, hospitals can cut down on wasted time by up to 30%, leading to happier patients.
Example #2 ➜ Faster Patient Discharges
Getting discharged from the hospital can often be a long, frustrating process with lots of paperwork and communication issues. Lean healthcare uses a method called Kaizen, which means “continuous improvement.” A team of healthcare workers reviews the discharge process, identifies inefficiencies, and makes changes like pre-discharge planning and electronic documentation. This can reduce the overall discharge time by 20-40%, freeing up beds for new patients more quickly.
Example #3 ➜ Faster Lab Test Results
Have you ever had to wait a long time for lab test results before your doctor could diagnose you or give you medication? Lean healthcare helps labs use a “Just-In-Time” approach, where they schedule tests based on demand rather than doing big batches. This way, they can speed up their processes and get results back 20-30% faster.
Example #4 ➜ Reducing Hospital-Acquired Infections
Nobody wants to go to the hospital and catch an infection! Lean healthcare uses Root Cause Analysis to identify the sources of hospital-acquired infections. Hospitals can then implement strategies like better equipment sterilization and improved hand hygiene to cut down on these harmful infections.
Pros and Cons of Lean Healthcare
Lean healthcare has many advantages if you can implement it in your healthcare practice. However, it also has some disadvantages that can be tackled by implementing correct strategies.

Pros of Lean Healthcare
✅ The main benefit of lean healthcare is that it removes waste and improves all medical processes. This makes operations more efficient. You can do this by cutting out extra steps, organizing patient movement, and making work processes simpler.
✅ Various lean methods help find and remove activities that do not add value, which can lower operational costs effectively. You can lower these costs by cutting down on inventory costs, waiting times, and using resources more efficiently.
✅ A good and balanced workplace is made by helping employees to notice and fix problems themselves. This can affect how happy people are with their jobs and make them work harder.
✅ Using lean healthcare methods helps make sure your patients receive care quickly and effectively. This can make patients happier and improve results.
✅ Using clear processes and good practices can help lean healthcare lower the chances of mistakes and make patient safety better.
Cons of Lean Healthcare
❌ Using lean methods means making big changes in culture and showing dedication in healthcare practices. But, resistance to change and not having support from healthcare staff can make it hard to implement things successfully.
❌ It can be hard to see how lean initiatives affect things when they are complicated. Keeping a complex system running needs better data gathering and examination.
❌ Focusing more on efficiency can sometimes cause people to ignore important human factors. But, not having this element can lead to staff tiredness and lower the quality of care.
❌ It can be hard to manage and keep lean healthcare practices working well for a long time. So, it is important to keep checking and putting these ideas into practice to maintain them in healthcare.
❌ Small healthcare practices might find it hard to manage resources. This is because starting lean processes can take more time, training, and money.
Conclusion
Are you keeping an eye on the current state of your practice? Lean healthcare allows you to concentrate on cutting waste and streamlining procedures to improve operations. This may result in patients receiving better care. Putting the patient first raises the standard of care and increases the flexibility of your medical business. By maximizing patient flow, it may maintain profitability while enhancing service delivery.
Optimize Patient Care with BellMedEx’s Lean Healthcare Solutions 🕊️
Our medical billing and RCM services are designed to align with lean healthcare methodologies, ensuring maximum value for your patients while minimizing waste. With our value stream mapping expertise, we’ll uncover inefficiencies and opportunities for improvement, empowering you to provide a truly patient-centered care experience.
Thanks to BellMedEx, our billing reimbursement is at its highest!
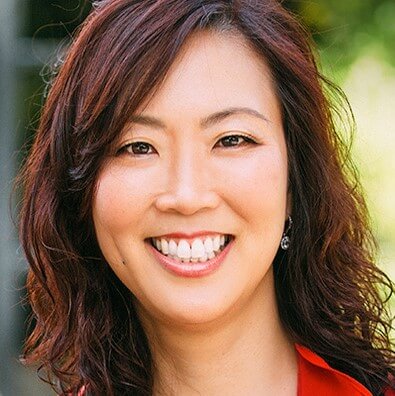
Dr. Esther
Counselor, Mental Health Clinic
Top Features
✓ Medical Billing Service
✓ Medical Coding Service
✓ Revenue Cycle Management